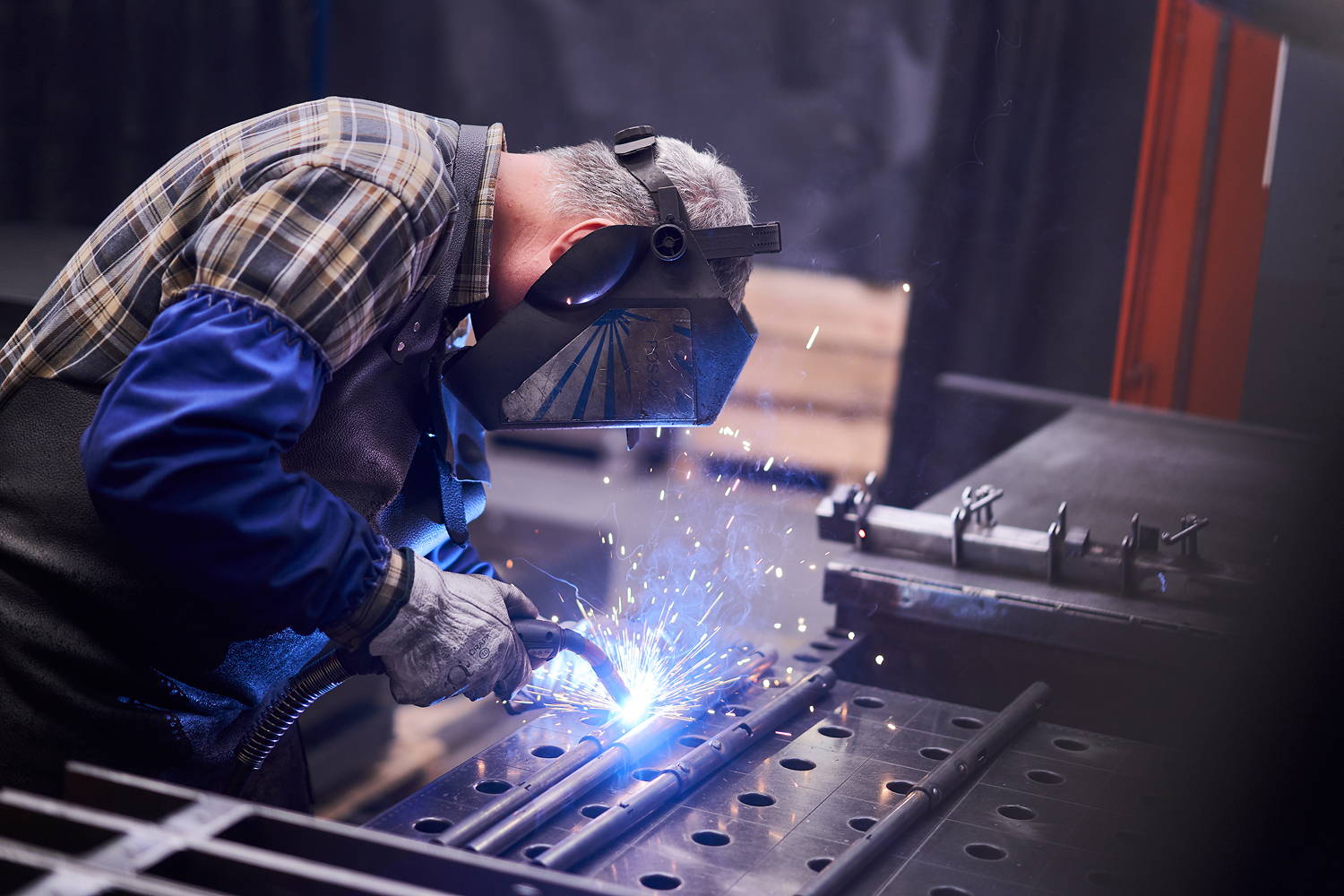
Go behind the scenes of Toom Modular Sofa production
Let us take you for a short stroll through the steel and upholstery factories we’ve teamed up with. Get a perspective of the production processes and see how they result in a perfect marriage of cutting-edge production technology and precise skills of human hands.
Modularity: the sky is the limit
The vanguard of its kind, Toom’s uniqueness derives from a smart and clean design, created out of two simple modules, which allow to build an endless number of configurations that can be easily changed over time.
After more than two years of extensive works on developing the final design, we created a truly modular sofa whose modularity has no limitations. At the same time, we are proud that such a complicated design process resulted in such a minimalist, simple in form solution, consisting only of eight components, which can meet many different expectations and suit a variety of spaces.
The production process was split between two factories: both have over 20 years of experience and both employ the best specialists, for whom the highest accuracy always comes first.


Steel processing: the beauty of repeatability
The first factory, specialized in metal processing, produces frames and metal parts used to assemble the sofa. The production processes that are taking place there are: precise laser cutting of steel, cutting holes used for assembly, welding of components with automatic welding machines, as well as grinding and powder coating, thanks to which the final components are resistant to mechanical damage.
The system of joining steel elements was developed by our designers in cooperation with the factory. Let’s say the beauty of Toom’s production and assembly lies in their repeatability – the production processes of the base module and the expansion module are exactly the same.
Most importantly, all modules must be identical, which is why it is very important to control them at each stage of their production. In case of frames, the components of the final product undergo four quality checks after each stage of the process. If they don’t meet the requirements, they return to the production line for improvement. This minimizes the risk of any manufacturing errors.


Upholstery production: tailored to the needs
While working on Toom Modular Sofa, noo.ma partnered with a new upholstery contractor. The factory was involved in the process of making the sofa from the very beginning. All design and implementation issues were consulted with them on an ongoing basis.
The factory is located in Poland (like most of the factories we work with), so our designers visited it often to test and prototype, and to ultimately come up with the product of the finest quality, down to the last centimeter.
Plywood forms, which constitute the base of the upholstery, are cut on CNC machines to maintain 100% repeatability of construction elements. As the most visible elements, Toom’s pillows are done by the best craftsmen – upholsterers and tailors who sew each of them according to strictly defined standards.


Optimization: #lesswaste is king
One of the main objectives when designing the sofa was to reduce the use of material and to provide the possibility of its reuse in case of damage. Each element can be replaced separately – when it’s damaged, there’s no need to manufacture a whole new product, only parts of the components.
Also, the usage of fabrics is optimized – after confirming the dimensions of the cushions, noo.ma's designers have developed such a way of using the pattern, that the entire width of the material is being used. What’s more, the filling of the cushions does not require cutting to obtain a specific form, so we always use exactly as much as we need, without large waste.

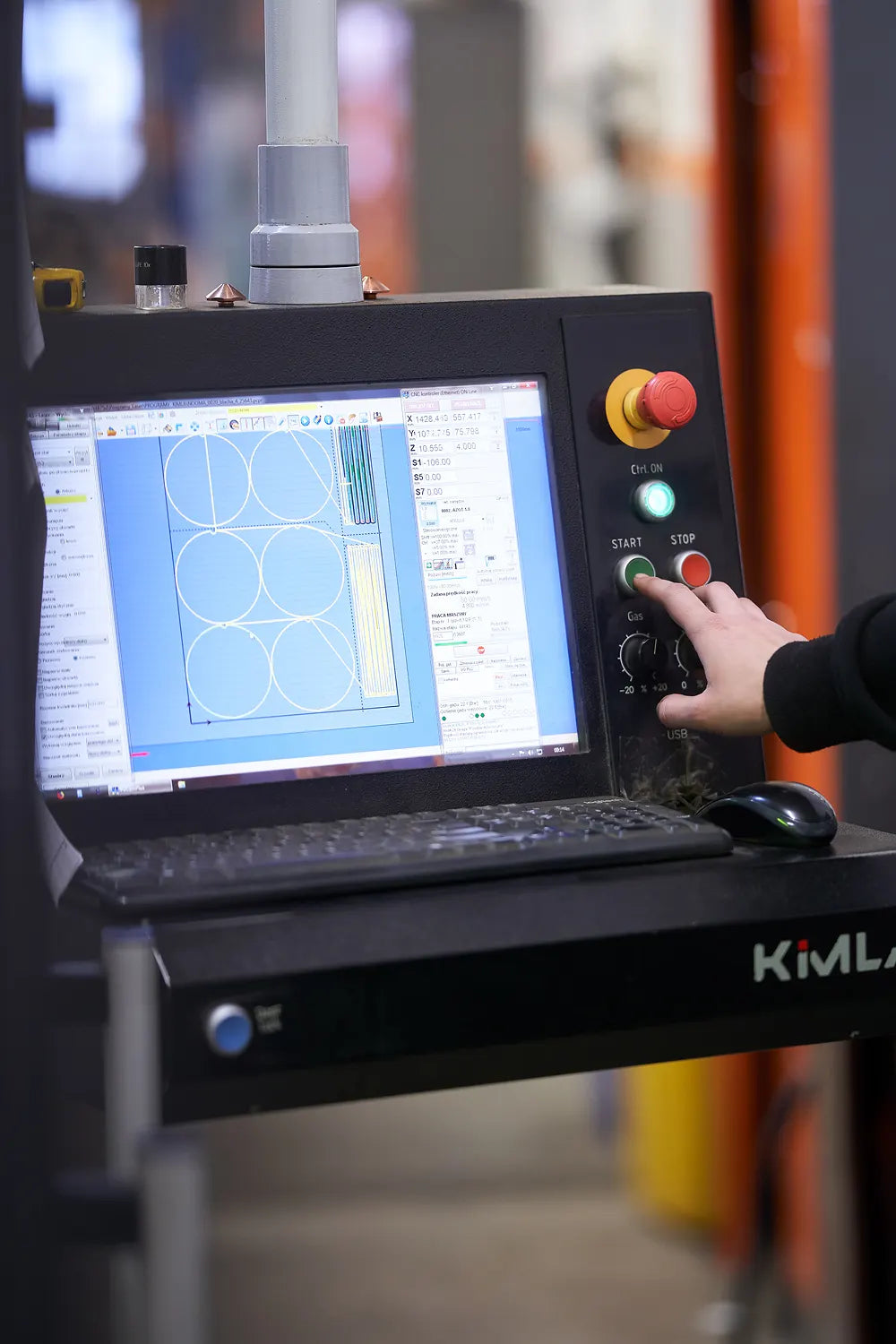
As a result, we’ve found the golden mean when it comes to the seat-depth and thickness of the sofa, which makes it incredibly comfortable if you want to relax, and appropriately balanced for more formal meetings. We call it a new-active comfort.
